据外媒报道,科克·菲尔普斯是卡邦3D打印公司的产品管理副总裁,这家公司开发出一种全新的持续液体界面生产技术,能够使3D打印机用新材料制造出耐用品。
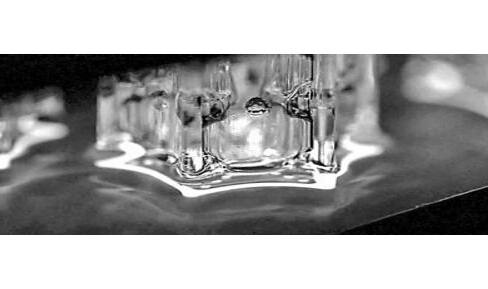
升级后的3D打印机利用光和氧气作为培育零部件的基础,打印材料采用树脂和合成橡胶,两者具有不同的机械性能。结合了新技术的打印机在制造零件时不是一层一层进行镀层切割或加工,而是通过软件来控制完成一个光化学过程。在聚合树脂液池中,打印机通过平衡紫外线与氧气之间的化学反应来打印物品,其表面比传统3D技术打印出来的更加光滑。
据研究人员介绍,新技术同时控制光合氧气进行打印,打印过程会产生一个很有趣的现象,即所要打印的物品是像活体一样从液体池中缓缓升起,而非一步一步被固体材料缓慢打印出来。原来新型3D打印机在树脂液池中会使树脂变硬塑形,而氧气则使之保持液体状态。随着池底部的氧气量加大,所需打印的物体在上升的过程中能够成型。
可以说,该公司在研究3D打印全过程时,弄清了背后的化学、物理过程,从而创造出一种几乎是在液体池中“生长”出物体的技术。这种技术从根本上就比传统技术更快,据计算,其打印速度几乎是同类产品的100倍。
研究人员认为,新技术和新材料能够让3D打印技术制造其他工艺无法加工的产品,私人定制也能实现。比如人们如今已经明白心脏状况如何以及其机械属性如何,了解这些情况后,新3D打印只需几十分钟就能打印出一款适合特定病人的3D打印心脏支架。
在过去的三年中,这项技术已从谷歌等资本投资公司获得了超过两亿四千万美元的支持,并且与福特、宝马和强生等大公司开展合作。目前该技术已经使用多种树脂材料制作出适用于不同场合的耐用品,譬如使用阻热硬树脂来打印汽车外部零件,以及使用柔软且弹性强的生物可降解树脂来制造心脏支架等医疗器械等。