Paulaner 啤酒厂开创了啤酒酿造的新纪元。

380多年来,Paulaner(柏龙)啤酒厂一直在慕尼黑奥区的诺克亨堡酿造其世界著名的啤酒。该啤酒厂以前位于城界之外,现在处于城市中心。目前,该企业在这里遭遇增长瓶颈,搬迁迫在眉睫。随着在慕尼黑朗维德区全新工厂的开业,Paulaner 成功完成了企业搬迁。除了两套糖化设备,克朗斯还提供全套流程设备,包括酵母系统、冷区、刷洗设备以及流程引导系统。“好,更好,Paulaner。”该啤酒厂现在利用斯坦尼克工艺酿造啤酒。
Paulaner 啤酒公司目前共有800 多名员工,其中约280 人从事新建厂的技术和物流工作。每年约30 万千升啤酒从这家经典巴伐利亚多品种啤酒厂的厂区运出,其中包括品牌Hacker-Pschorr。目前,一半产量为小麦啤酒系列,包括七种不同的小麦啤酒。例如,天然浑浊酵母小麦啤酒在全国市场占据主导地位。此外,还酿造慕尼黑系列的五种下面发酵啤酒,例如,慕尼黑浅色,慕尼黑Urtyp。另外,还包括一些特色产品:Salvator,这是德国销量最高的超级烈性啤酒,也是所有烈性啤酒的鼻祖;十月节啤酒,慕尼黑比尔森;无醇饮料,例如,Paulaner Spezi 和Paulaner 酵母小麦无醇(Paulaner 于1986 年推出的全球第一种无醇小麦啤酒),为丰富的品种画上了圆满句号。
需求持续增长带来的“快乐烦恼”
“增长,基础设施改善,劳动保护,可持续,工作流程的效率和质量。”这是企业搬迁的主要原因。这次搬迁对于慕尼黑具有更重要的意义,因为Paulaner 是慕尼黑到目前为止唯一一家还在原来厂址酿造啤酒的啤酒厂 — 而且还是一家创建于1634年的啤酒厂。由于地处慕尼黑诺克亨堡的狭窄城区,工厂在夏季经常遭遇产能瓶颈。如果目前实施的增长计划得以实现,就很可能突破这些局限。“我们当时有一个快乐的烦恼。”Paulaner啤酒厂负责供应链的执行董事Stefan Lustig 博士解释说。“在国内,尤其是在国外,对我们啤酒的需求都呈现出持续增长。对此,我们就是没有足够的场地。”为了满足未来的需求,Paulaner 决定在慕尼黑黑朗维德区投资建造新厂。在2015年,这家新建工厂是慕尼黑最大的啤酒厂,它将经典的慕尼黑酿造传统与最新、最环保的啤酒厂设备结合在一起,从而为Paulaner 在慕尼黑续写成功历史奠定了基础。
Paulaner 啤酒厂提出的要求是将传统的酿酒艺术与高度现代化的设备融合在一起。
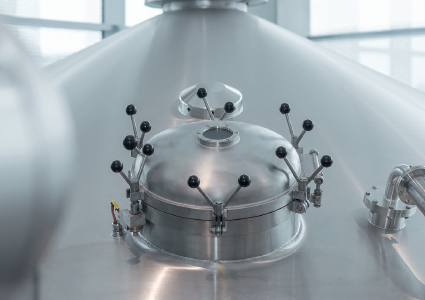
2014年初,厂区内开始土建工作,6月份奠基。同期,克朗斯获得全部啤酒生产设备的合同。2014年8月至11月,发酵罐和后储罐到货,11 月就已经开始安装糖化设备。在33米高的糖化烟囱的最上部为游隼布置了一个鸟巢,这和以前位于诺克亨堡的啤酒厂一样。2015年8月14 日,在新建啤酒厂举办了Paulaner 酿酒师和Paulaner 原始酵母的搬迁庆典仪式。两个星期之后,糖化首次投料。“第一次投料结束后,我们与克朗斯现场负责人一起举办了传统的雪茄仪式。在那一天,我们临时取消了糖化车间严禁吸烟的规定。”Stefan Lustig博士透露。过滤车间于2015年10月初第一次投入运行。
2016年初,朗维德工厂全部投入生产,而诺克亨堡老厂于3月彻底停产。水处理包括采用最现代化膜过滤工艺的克朗斯Hydronomic 、三个紫外线杀菌单元、一台能力为每小时55 立方的脱氧水单元以及一个存放脱氧水的暂存罐。
新厂占地15公顷,每年可以生产35万千升啤酒,比以前位于诺克亨堡的啤酒厂产能大约提高15%。为了进一步实现增长以及根据市场情况灵活做出反应,已经在一份整体规划中考虑今后将产能提升到50万千升。目前,安装了两套回收玻璃瓶设备、一条回收玻璃瓶和一次性玻璃瓶两用线、一套纯一次性玻璃瓶设备、一套易拉罐设备以及一套桶装设备。
可持续能源方案
多年来,Paulaner始终按照DIN ISO 14001环保管理体系工作。2013年秋季,该企业首次通过欧盟内部最严格的最高环保标准EMAS III 认证。借助新厂,这项方针被持续贯彻:在慕尼黑市郊,出现了一家欧洲最环保的啤酒厂。酿酒需要的能源大部分自己制备。“我们基本上采用高压热水作为加热介质,因为我们认为这是热能传递最高效的方式。我们采用了斯坦尼克所能提供的全部能源回收技术。此外,为了通过燃气高效产生电流和热能来保证啤酒厂的能源供给,我们决定安装两套热电联供设备。借助我们污水处理设备产生的沼气,我们可以获得20%至25%的初级能源。总体上看,我们为啤酒厂选择了这样一个现代化的能源方案,它一方面可以珍惜资源,另一方面,还可以带来经济效益。我认为,我们的能源消耗指标可以进入欧洲啤酒厂的前三位。”StefanLustig博士表示。
Paulaner是德国为数不多的几家采用自有沼气设备的啤酒企业,该啤酒厂通过处理酿造流程的污水从沼气中获取能源。伴随着无醇啤酒的潮流,这种设备具有更重要的意义:无醇小麦啤酒首先采用传统的方式酿制,之后才将酒精脱掉。这些酒精被送到沼气设备,重新为啤酒酿造提供能源。这样,生产无醇小麦啤酒大约84% 的热能来自最初包含在啤酒中的酒精。
Paulaner啤酒厂60%的电能通过两套热电联供设备由自己产生。水耗方面与此类似:从全球范围看,每百升成品啤酒耗水3.5百升已经是一个非常好的指标。当时位于诺克亨堡的工厂已经达到了这个指标,朗维德的新厂还将继续降低。按照最新工艺标准制造的高效设备可以确保Paulaner 啤酒厂更加珍惜地使用天然资源。
传统酿酒艺术与高度现代化的设备
Paulaner啤酒厂提出的要求是将传统的酿酒艺术与高度现代化的设备融合在一起。对此,Paulaner委托克朗斯作为生产和流程设备的总承包商,分界点一个是能源供应,另一个为清酒间或者灌装车间。克朗斯提供全部工艺装备,包括两套糖化设备、酵母间、发酵和后储、过滤、清酒。“斯坦尼克的出名之处,一方面体现在工艺领先地位,例如,Pegasus麦汁过滤工艺和Stromboli麦汁加热器,另一方面也体现在始终忠于经典的慕尼黑酿造方式。”Stefan Lustig博士表示,他毕业于魏恩施蒂芬大学的酿酒工程专业。“斯坦尼克的工艺技术让我们信服,因此,我们的决策相对比较容易。我们在选择工艺时非常重视继续保持我们在诺克亨堡工厂原有的工艺。此外,从新厂的调试和达产到老企业的停产,时间间隔比较短,因此我们必须尽量避免在质量和口味方面的风险。基于这些原因,我们为成熟、经典的巴伐利亚双醪煮出工艺采用糖化锅加糊化锅的配置,这也是Paulaner 口味特色的一个原因。”
“ 我们期待Evoguard 阀门能够保证全自动运行流程的最高微生物可靠性”,Stefan Lustig 博士强调。
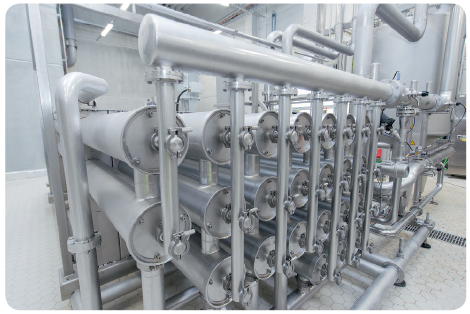
为了保证质量和设备产能,过滤槽选择了较大的过滤面积。“我们最后选择了Stromboli麦汁煮沸系统,它可以变化调节,还能在设备的加热流程和蒸发率以及能源效率之间找到准确的平衡。”Stefan Lustig博士说,“借助斯坦尼克糖化设备,我们找到了控制所有这一切的操纵杆。我们现在使用相同的原料,采用类似的糖化设备,只是尺寸略有变化,此外,我们还和克朗斯一起将诺克亨堡工厂的酵母系统一比一地复制过来,既包括下面发酵生产,也包括上面发酵。发酵罐的尺寸变化也不大。我认为这些都是保持我们啤酒口味不变和质量的关键因素。”
两条相同的糖化线
两条相同的糖化线每天可以分别完成10次糖化,每次糖化的产能为90至98 立方热麦汁。两台Powermill湿粉碎机每小时可以分别为每条糖化线粉碎40 吨麦芽。这是Paulaner的一项创新:诺克亨堡老厂采用的标准是干粉碎。“我们期望湿粉碎在麦芽净化、除尘和输送方面具有更加直观的花费。另外,这是一种工艺可靠、质量优良的投料方式。”Stefan Lustig博士说。每条糖化线配备两台ShakesBeer糖化器皿,一台为糖化锅,另一台为糊化锅,采用传统的双醪工艺。两台Pegasus C过滤槽的直径均为11.5米,容量210立方,在德国啤酒行业已经属于最大的过滤槽。它代表了糖化车间的核心部分。设备的进一步研发,包括耕糟装置的改进,有针对性地优化了洗糟效果。
每条糖化线还包括一台煮沸锅、一台回旋槽、一台麦汁暂存罐和一套用于调节PH 值的酸化设备和一台酸化罐。麦汁煮沸锅按照低压煮沸设计,配备Stromboli 内加热器。“我们坚信,我们通过Stromboli 可以取得良好的蒸发效果,同时还可以实现3%至4%的蒸发率。”Stefan Lustig博士解释说。每条糖化线配备一台乏汽冷凝器和一台容量为140立方的储能罐,用于热能回收。此外,在流程设备中还安装了用于为冷凝水降温的板式换热器(包括一台冷凝水罐)、一台用于麦汁预热的板式换热器、一台热凝固物罐、一台产能为每小时120立方的两段式麦汁冷却器以及三台酒糟销售罐。酒花添加设备分别由一台颗粒酒花和酒花浸膏自动添加装置组成。
Pegasus C 过滤槽的进一步研发,包括耕糟装置的改进, 有针对性地优化了洗糟效果。
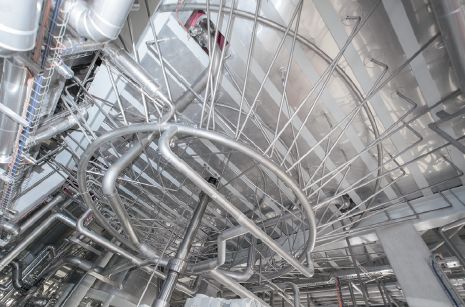
这套斯坦尼克酵母设备既可以用于上面发酵酵母也能用于下面发酵酵母,包括相应的酵母存放系统:四台圆柱形锥底酵母罐、两台浓酵母罐、两台废酵母罐和两台残酒罐。斯坦尼克还提供全套的CIP设备,总计配备十个储罐以及化学药品自动添加装置。
发酵设备全自动运行
发酵和后储间分为8个发酵和后储区,共计采用63个大罐。这些大罐按照隔间式罐区系统设计,采用室内降温,不需要冷带。包括清酒罐区,Evoguard双座阀可以确保无泄漏的切换。“我们期待Evoguard 阀门能够保证全自动运行流程中方最高微生物的可靠性。”StefanLustig博士强调,“对于 Paulaner啤酒厂,这种全自动化系统是一种新的运行方式。我们以前在诺克亨堡老厂还是通过许多跨接管和软管对发酵间采用人工操作,现在我们由双座阀过渡到全部自动运行。我们坚信,我们可以通过阀门和流程技术实现更高的微生物可靠性。另一方面,通过现代化的阀门结构和相应的密封技术,维护保养工作也具有重要意义。我们将通过主动调整、预防性维护来延长使用寿命。目前来看,Evoguard的使用效果非常不错。”
从麦芽进料到灌装的全部自动化流程由Botec F1流程引导系统控制。在发酵间,路径控制工具DynaRoute负责设备安全。这种软件根据设定的程序自己寻找可以利用的管路途径,为发酵间的产品输送确定起源地和目的地之间的连接。作为这种系统的真正大脑,路径控制器考察设备状况,检查哪些介质位于哪些管路,控制和协调这些路径,记录这些流程。“这对于我们的员工来说也是非常大的改变。
在诺克亨堡老厂,还是按照传统方式将糖化、发酵和过滤分成独立的区域,员工具有明确的分工,现在我们从唯一的一个控制室监控全部流程。这为员工开辟了一个全新的世界,Botec和DynaRoute自动化系统对此提供很多帮助,”Stefan Lustig博士评价说。
啤酒酿造的新纪元
Paulaner 啤酒厂的过滤由一套不需要硅藻土的膜过滤设备组成。生产小麦啤酒时使用离心机。新啤酒厂的水处理设备也属于克朗斯的合同范围。这套设备包括采用最现代化膜过滤工艺的水处理设备Hydronomic 、三个紫外线杀菌单元、一台产能为每小时55 立方的脱氧水单元以及一个存放脱氧水的暂存罐。这里采用的Hydronomic 是当前产能最大的水处理设备之一。
除了上述设备,克朗斯还负责安装全部管路系统。“这是一个令人振奋的项目,面临许多挑战。对于我个人来说,这是我职业生涯最美的好时光。我相信,能够参与这种新建项目,是每一个酿酒人的梦想。对于我们这一代人,德国并没有很多酿酒工程师能够享受到这种机会。”Stefan Lustig博士对此表示感谢。