导读:使用软件去模拟一块或多块部件运行是汽车制造工业不可或缺的组成部分,这被称为“虚拟调试”。下面我们来看看美国中西部一家食品生产商是如何通过提升其三条包装生产线生产能力来满足其增产需求的。
当前最重要的问题在于如何处理食品生产商遗留的包装线设备,但无法确定某些设备瓶颈,而且也缺乏固定这些设备所需要的投资。为此,聘请了伯恩斯&麦克唐奈公司(Burns & McDonnell)堪萨斯城分公司参与该工程,该公司是一家总部位于密苏里州的设计和工程公司。他们使用罗克韦尔自动化领域的软件模拟了现有包装线操作。Arena仿真使用一种“假定分析—确定模型”,采用单点估算法;包装线中的不确定变量被赋予了一个最可能的估计值。
伯恩斯&麦克唐奈公司使用现有的生产数据模拟了这三个包装线,发现一些设备运行不佳。伯恩斯&麦克唐奈公司根据工厂生产能力、生产计划、设备可靠性数据、设备等级和能力来创建模拟生产线。
根据伯恩斯&麦克唐奈公司的建议,模拟过程中使用了生产数据来确定各个包装设备的范围。“根据前六个月的工厂基础数据,仿真软件能准确模拟150天的工厂基础产量。”伯恩斯&麦克唐奈公司的工业工程师Abbey Hatke说。“这些结果包括设备的可靠性和生产线的可靠性,并且误差在0.25%范围内,我们的团队已经创建了一个现实的工厂环境来测试其模拟实验”。
筛选工厂数据后,食品制造商针对42种不同情境进行测试和评估,并单独分析了打包机、封瓶机、成型机和码垛机。伯恩斯&麦克唐奈公司采集了每台设备的操作范围并且估算了120天的平均生产能力。
因此,食品公司避免以高昂的代价重新构建包装线,转而用特定设备取代。三条新生产线的总成本到达了1800万美元,但是停工期缩短了80%。据伯恩斯&麦克唐奈公司称,这意味着公司所追求和更需要的生产能力提高了百分之十。
(cpmin翻译,转载请注明)
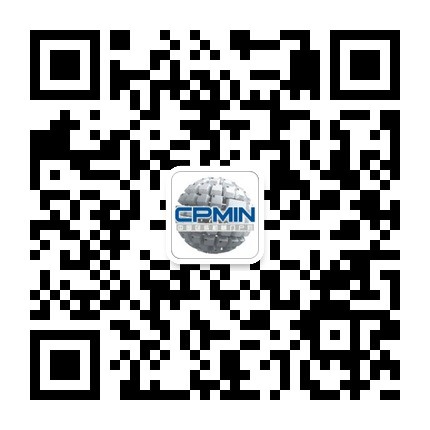
官方微信二维码